It is almost a cliché to say that now more than ever, owners and operators must conserve resources, as money is getting not only tighter but is being taken back and reduced by payers. What’s more, poor quality is expensive: The Institute of Medicine (IOM) estimates that preventable medical errors kill as many as 98,000 patients annually. However, in almost all of these cases, it is not incompetent caregivers or lack of compassion that causes these errors, but rather the complexity of the health care delivery system.
Errors resulting from a failure to address deficiencies within the care delivery system cost hospitals an estimated $17 billion to $29 billion per year nationwide, according to IOM. Financial costs, however, are not the only penalty paid by facilities for medical errors. The effect on staff morale and public perception is immeasurable.
TPS And Lean
One company that struggled with a similar issue and solved the problem is Toyota Motor Sales Co., and the system it developed is known as the Toyota Production System, or TPS.
Toyota was established in Japan in April 1950. The decision to launch an enterprise in post–World War II Japan, when Japanese products had a reputation for shoddy workmanship, should most certainly have resulted in failure.
Taiichi Ohno, a vice president at Toyota, was sent to the United States to study Western manufacturing methods. More specifically, Ohno studied what was at the time a revolutionary concept for manufacturing, the assembly line used by the Ford Motor Co.
Using the ideas developed by Ford, Ohno developed a revolutionary concept of his own, and today is credited with the development of the now famous TPS, which incorporates the practice of eliminating waste, or becoming a “Lean” company.
The interesting thing about waste is that it likes to hide. It disguises itself as work and is difficult to distinguish from the real thing. Like an iceberg, however, the portion that appears on the surface is minuscule, compared with the portion that lies beneath. As one starts to chip away at surface waste, more and more waste is exposed. By continuing to eliminate this waste as it is uncovered, an organization will become Lean.
The
Lean principles derived from TPS have been revolutionizing the manufacturing and service industries worldwide for many years (
see Figure 1, above).
Lean can create a balance between quality and finance by developing the most efficient and effective method of providing value to customers. TPS grew out of a disheartening situation, similar in some ways to the experience of many hospitals today. However, by internalizing the basic principles of Lean, Toyota has become today’s quality leader, and health care can do the same.
A War On Waste
The Toyota name has become synonymous with quality. But an awareness of the unstable beginnings of Toyota is fundamental to an understanding of how Lean principles can help create a balance between quality and financial stability in health care.
What did Taiichi Ohno do that made such a difference? He declared war on waste in the workplace. Wasteful practices occur every day in factories, offices, and hospitals worldwide.
By declaring war on waste in the workplace, he was able to cut costs and focus on quality. In fact, Ohno was so consumed with the idea of eliminating workplace waste that he is recognized in the book “Lean Thinking” as “the most ferocious foe of waste human history has produced” (Womack & Jones, 1996).
Waste is anything that does not add value to a product or service from the standpoint of the customer (Womack & Jones, 1996). In a health care setting, value might be described as comfort, compassion, competent caregivers, or being discharged after desired outcomes have been achieved. By classifying work as value-added or non-value-added, waste can then be exposed and eliminated.
It is astonishing that in most organizations only about 10 percent of the daily work being performed is value-added. Some sources put the number as low as 5 percent, while the other 90 percent of the work being performed falls into the category of Type 1 or Type 2 non-value-added activities (see Table 1, below).
By eliminating as many of these non-value-added work actions as possible, an organization can become significantly more profitable.
Table 1: Lean Work Classifications
1. Value-added |
A work-related action provides valude from the standpoint of the customer. |
2. Non-value-added, Type 1 |
Does not add value to product, but is necessary. |
3. Non-value-added, Type 2 |
Actions that do note provide value. |
---|
A simple business formula indicates that price is equal to costs plus any profit made on the product or service. By eliminating waste related to these actions, Toyota found that quality was enhanced, productivity skyrocketed, and costs plummeted.
Managers in many organizations observe that their employees are busy all day, work late, and may even bring work home with them or come in on weekends. Being busy, however, is not necessarily adding value. Employees can be busy 110 percent of the time, but if what they are doing is not adding value from the standpoint of the customer, it is considered waste.
Identifying Waste
Identifying and eliminating waste may appear relatively simple, but the process involves a surprisingly difficult interim step. Acknowledging that something is indeed waste is undoubtedly the biggest barrier to overcome when implementing a Lean transformation.
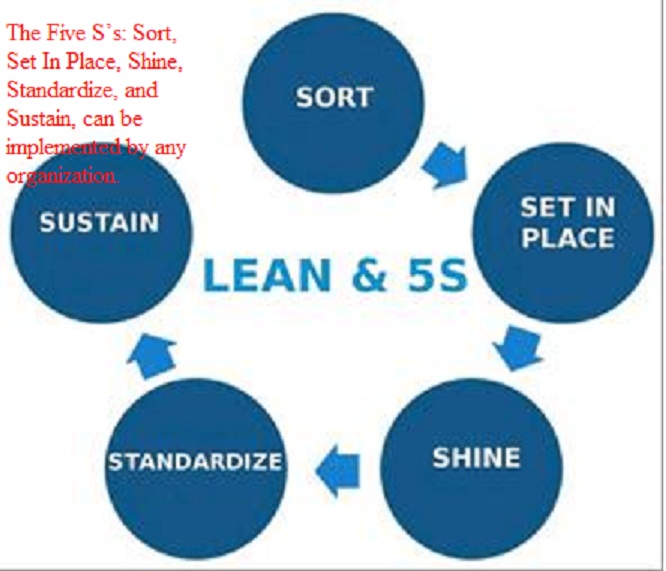
Many people are reluctant to view the work they have been performing for many years as wasteful. Accordingly, they become defensive and resist any effort on management’s part to change the situation.
Most waste develops as a result of stopgap measures, which are typically devised and implemented to provide a temporary solution to a problem. As time passes, the stopgap measure becomes “the way we’ve always done it” and is institutionalized. Anyone questioning this process would be told that “this is the way we’ve always done it.”
One effective process for eliminating waste is a tool known as the Five S’s: Sort, Set in Place, Shine, Standardize, and Sustain, which can be implemented by any organization to create a solid foundation for future Lean initiatives (see Figure 2, above).
Also useful are
kanban tools, a mechanism that uses cards to signal when something is needed or needs to be done. For example, a hospital in Seattle and all of its campuses in the Seattle area implemented a kanban system, which signals the need to restock. Kanban, which means “visual card” in Japanese, uses exactly that—a card put near the bottom of a pile of tongue dispensers, gauze strips, or brochures, for example. When a nurse or physician sees the card, he or she knows it’s time to refill. Supplies don’t run out, but they also aren’t over-ordered.
Lean Applications In Health Care
St. Clair Hospital, outside of Pittsburgh, successfully converted its par system for replenishing nursing supplies to a two-bin kanban system. This
video is a brief overview of their process and the impact the change had on nursing staff.
Seattle’s Virginia Mason hospital discovered TPS and Lean several years ago and has since tailored the Japanese model to fit its needs. Read more about it
here.
These techniques may seem too simple to be effective, and they are simple—but they are not easy. If they were easy, every organization would be a Lean organization. The desire to cling to the familiar, fear of change, and lack of understanding make creating a Lean organization difficult and sustaining it even more difficult.
Table 2: Traditional Culture Vs. Lean Culture
Function Silos |
Interdisciplinary teams |
Benchmark to justify not improving: "Just as good." |
Seek the ultimate performance, the absence of waste. |
Blame people |
Root-cause analysis |
Rewards: individual |
Rewards: group sharing |
Supplier is enemy |
Supplier is ally |
Guard information |
Share information |
Volume lowers cost |
Removing waste lowers cost |
Insurance companies, as well as government entities, are not willing to pay for the non-value-added work associated with health care processes. In addition, external forces such as reimbursement issues, staffing shortages, rising costs, and others mean that health care organizations need to ensure that their processes are devoid of as much non-value-added work as possible.
Learning and using some of these simple techniques can eliminate areas of waste and increase value-added services.